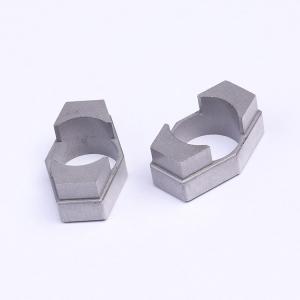
Add to Cart
professional accessories parts high powder metallurgy Machinery
Product Description
Oil-retaining Bearing | ||||
Material | Fe | Copper | CuFe | |
pretreatment of powder | Mixing | Adding lubricant | ||
Powder preparation methods | Atomization Method | Reduction Method | ||
Methods of formaing | Pressure Forming | |||
Material of Moulds | Steel Mould | Hard Alloy Mould | ||
Types of Moulds | Compression Mould | Finishing Mould | ||
Sintering Methods | Solid phase sintering | |||
Sintering Atmosphere | Cracked Ammonia | |||
Sintering Temperature | 700-1100℃ | 1050-2000℃ | ||
Compacting Methods | One-way Moulded | |||
Aftertreatment | Vacuum Oil Filling | Finishing |
ADVANTAGES OF POWDER METALLURGY PROCESS
· Do not need or only very little machining
· High usage rate of material(more than 95%)
· Parts size consistency is good and stable. The precision can reach 0.01mm.
· The material composition can be adjusted according to the customers’requirement of the parts performance.
· Do the treatment on the surface of the parts according to customers’ requirement to improve the strength and hardness.
· Due to the die forming, we can customize the complex shape or special profiled parts which other machining can not do.
· Because suitable for mass production, the production efficiency is high and the cost is lower than machining.